Stall Detection
FarmBot Express motor load detection settings.
Open these settings in the app
For FarmBot Express bots only
Stall detection settings are only available for FarmBot Express bots. FarmBot Genesis users should refer to the encoders section.
The stall detection feature for FarmBot Express bots utilizes the Trinamic TMC2130 stepper drivers’ capability of measuring back-current as a way of determining motor load, and thus when a stall has occurred. For more details, see the stall detection hardware page.
Enable stall detection
Enable use of motor stall detection for detecting missed steps, finding axis length, and finding home.
Recommended for the X and Y axes only
Stall detection is not recommended for use with the Z-axis due to the high motor load associated with raising the Z-axis against gravity.
Max motor load
Maximum motor load (out of 100) as determined by the stepper driver before a motor is considered to have stalled. Should be set high enough to prevent false stall detections and low enough to ensure that when the bot does stall, it is correctly detected.
Tuning stall detection
Every installation will have different characteristics that require the stall detection and motor settings to be tuned for optimal stall detection performance. The goals of tuning are to:
- Reliably detect when the FarmBot has stalled due to running into an obstruction, finding the home position, or finding the axis length.
- Avoid false stall detections during normal movements.
To achieve both of these goals, the realtime motor load must stay below the MAX MOTOR LOAD during a normal movement and exceed the MAX MOTOR LOAD when the motor has truly stalled. To view the latest, max, and average motor load readings in realtime, click the motor load indicator in the controls popup.
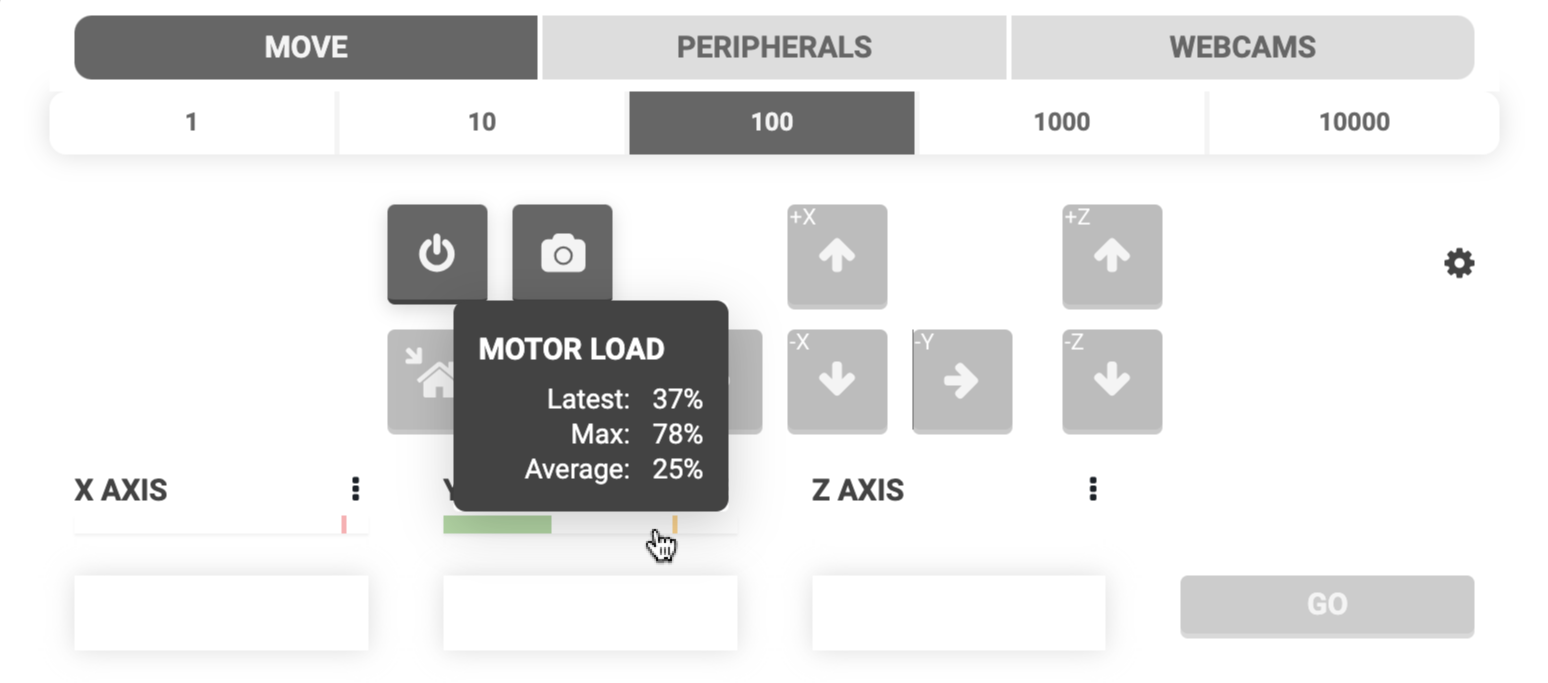
To view a plot of the motor load over time, click the icon in the controls popup and turn on the MOTOR LOAD plot. The horizontal dashed lines represent the MAX MOTOR LOAD for each axis, allowing you to visually see when the realtime motor load has exceeded the max threshold.
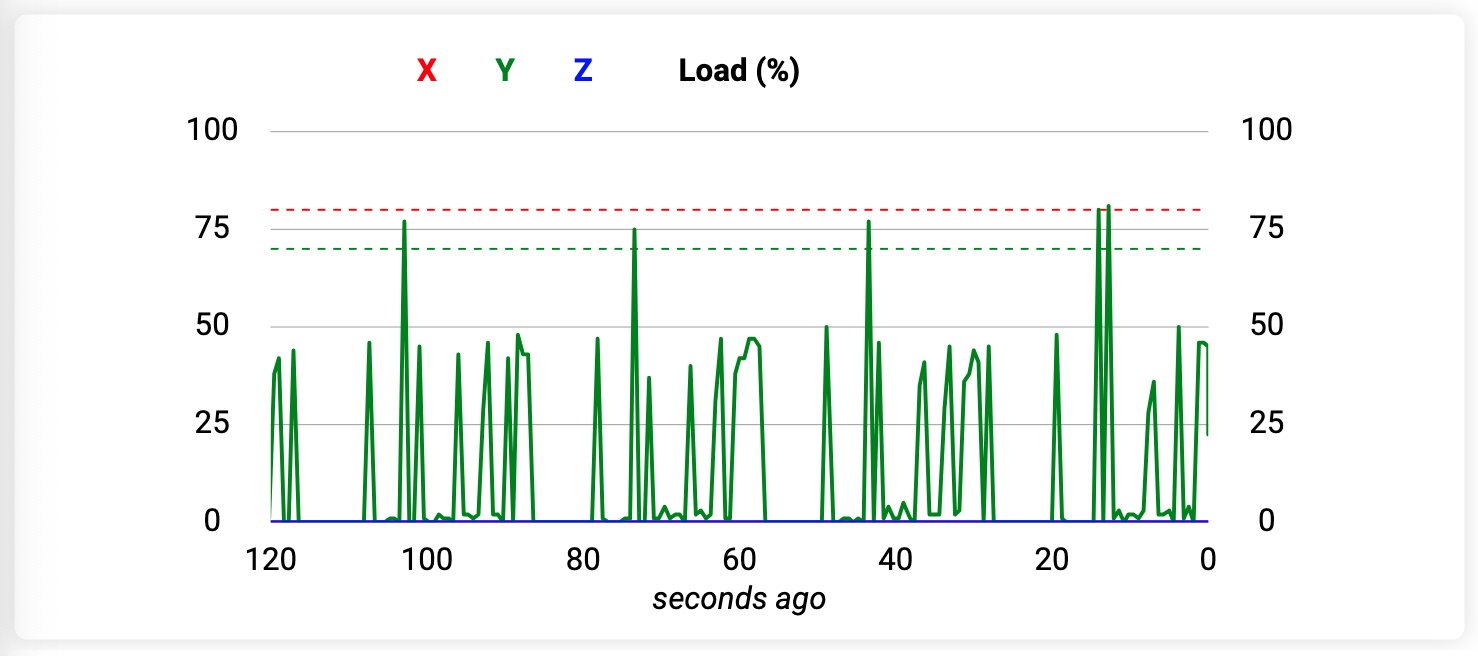
Adjusting max motor load
If your FarmBot is falsely detecting stalls during normal movements, try increasing MAX MOTOR LOAD in increments of 5. If your FarmBot is not detecting stalls when it should, try decreasing MAX MOTOR LOAD in increments of 5. Make sure to test various movement conditions after making changes:
- Movements in the positive and negative direction
- Movements at various locations along an axis
- Finding home and finding axis length
- Holding the FarmBot by hand to create a real stall
Adjusting speed and acceleration
If adjusting MAX MOTOR LOAD does not improve stall detection performance, try adjusting the motor speed and acceleration settings.
The motor load readings are very sensitive to the motor’s speed, where the load will be significantly greater whenever the motor is moving slowly (less than about 80 mm/s). This will be especially true during the acceleration and deceleration phases of a movement.
Once the motor is moving more quickly (80 mm/s or faster) the stepper driver will detect a lower load. Reducing the time spent traveling slower than 80 mm/s can be achieved best by shortening the ACCELERATE FOR distance in increments of 5 and increasing the MINIMUM SPEED in increments of 5. It can also be affected by increasing the MAXIMUM SPEED, though to a lesser effect.
Keep in mind that it is unreasonable to accelerate over an extremely short distance because the motors must bring the mass of the entire gantry up to speed. Accelerating too quickly or having a minimum speed that is too high will cause abrupt changes in speed that will compromise accuracy.
Turning off stall detection
If you cannot find settings that give good results for all movement scenarios, you may disable stall detection. Keep in mind that you will need to manually set the home position any time the FarmBot stalls due to an obstruction or if the FarmBot ever loses power and reboots.